Anodic aluminum oxide (AAO) is a nanostructured, self-organised porous material with a honeycomb-like structure. It serves as a cost-effective nanofabrication template across various disciplines within science and engineering. In this blog, we will talk about our latest study on AAO fabrication for superior nanofluidic systems.
Why is AAO beneficial for the TRANSLATE project?
AAO is an Earth-abundant and cheap material, with straight nanochannels parallel to each other. The diameter of these channels can vary from 10-15 nm to hundreds of nanometers, expanding the range of possible applications significantly. In the TRANSLATE project, we’re creating a nanofluidic system using nanoporous anodic alumina membranes. These membranes are filled with a solution containing sodium salt to transform low-quality waste heat into usable electrical energy.
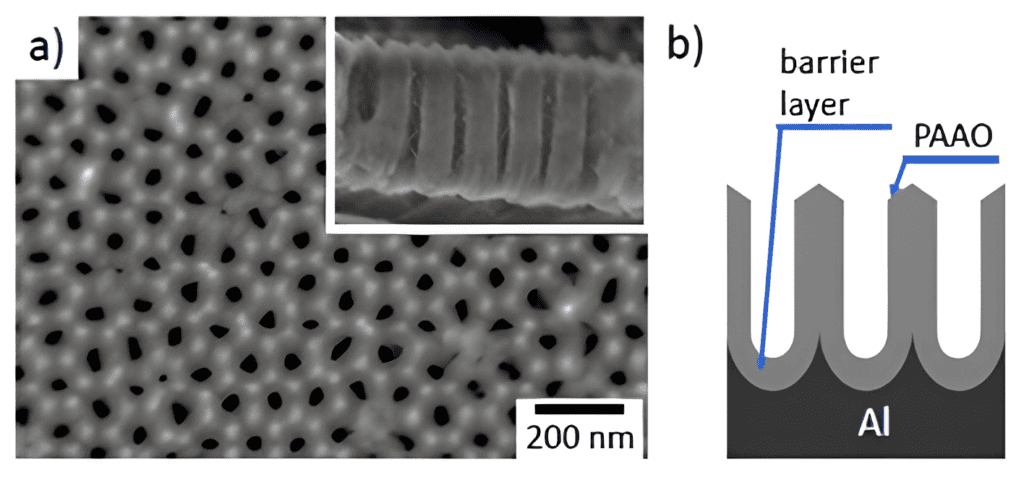
Challenges faced while fabrication of AAO
The uniform and parallel cylindrical nanochannels of anodic alumina are formed by the electrochemical oxidation of aluminum foil in acidic aqueous electrolytes. Usually, the AAO thickness is determined by the anodisation time and growth rate. While thickness accuracy can be enhanced through slow anodisation at lower temperatures, the spontaneous formation of oxide during the initial stages of AAO growth means that relying solely on process timing isn’t enough to ensure the desired outcome. Furthermore, the growth rate of the AAO can be influenced by many other factors, including local heating, electrolyte flow, arrangement of the electrodes, and crystallographic orientation of the aluminum substrate. It often takes a long time to determine the exact anodising time needed to obtain the AAO layer thickness.
Challenge accepted!
Based on many years of experience, the University of Latvia (UL) team applied a comprehensive approach to fabricating anodised alumina from ultra-thin films to membranes with a thickness of more than 100 microns. A thermostated electrochemical cell with an optical window was designed for in situ reflectance spectroscopy. The reflectance spectrum was continuously recorded from the AAO-coated aluminum surface during anodisation. The AAO thickness was calculated in real-time by fitting the spectrum to a multi-layer model of a water-AAO-Aluminum system using the transfer-matrix method (TMM). Real-time fitting of spectra to a transfer matrix model enabled continuous monitoring of the thickness growth of the AAO layer. Automation software was designed to terminate the anodisation process at preset AAO thickness values.
The thickness values obtained after optically controlled anodisation were confirmed using different methods, including spectroscopic ellipsometry and scanning electron microscopy, showing 1-2 nm variation within each sample. However, the greatest advantage of the new method is its non-invasiveness, which means it is possible to determine the thickness of the AAO layer without breaking or slicing the membrane! This makes it particularly suitable for quality control in the fabrication of AAO membranes for various applications.
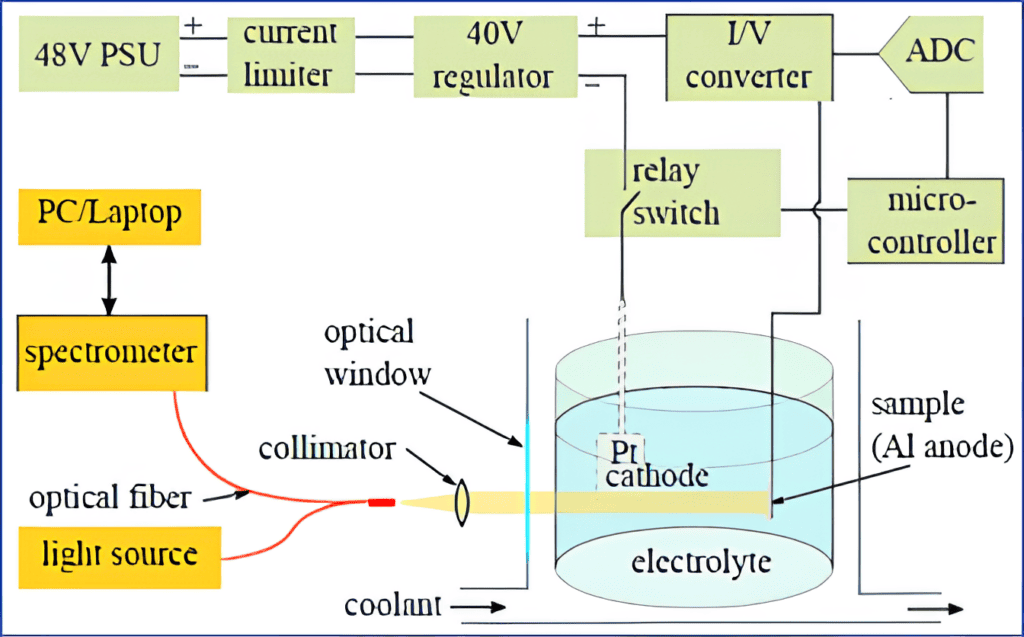
New opportunities for known material
Even though AAO is a well-studied material and much about its properties and fabrication process is already known, there always remains room for improvement. This simple and well-known material has the potential to become part of the novel energy-conversion technology by combining its environment-friendly nature with the benefits of nanoporous structure.
The above is the simplified version of one of TRANSLATE’s latest paper led by University of Latvia. More details can be found in the recently published open-access article: Dutovs, A.; Poplausks, R.; Putans, O.; Perkanuks, V.; Jurkevičiūte, A.; Tamulevičius, T.; Malinovskis, U.; Olyshevets, I.; Erts, D.; Prikulis, J. In-situ optical sub-wavelength thickness control of porous anodic aluminum oxide. Beilstein J. Nanotechnol. 2024, 15, 126–133. https://doi.org/10.3762/bjnano.15.12
Related reading: Functionalising Nanochannel Membranes
Find us on X, LinkedIn and YouTube for more interesting updates!